Discovering the Value of Welding Inspection in Industrial Applications: Protecting Against Failures and Enhancing Long Life
Welding evaluation offers as a crucial line of protection in commercial applications, making sure the architectural honesty and integrity of bonded components. By methodically identifying defects such as porosity and insufficient fusion, inspections not only prevent failures however likewise extend the lifespan of vital properties.
Function of Welding Evaluation
Welding examination works as a critical protect in industrial applications, making sure that bonded structures fulfill defined requirements of quality and safety and security. This process includes an organized assessment of welds to verify their honesty, toughness, and conformity with recognized codes and specifications. The role of welding examination is diverse, incorporating both aesthetic evaluations and non-destructive testing techniques, which might consist of ultrasonic, radiographic, or magnetic bit screening.
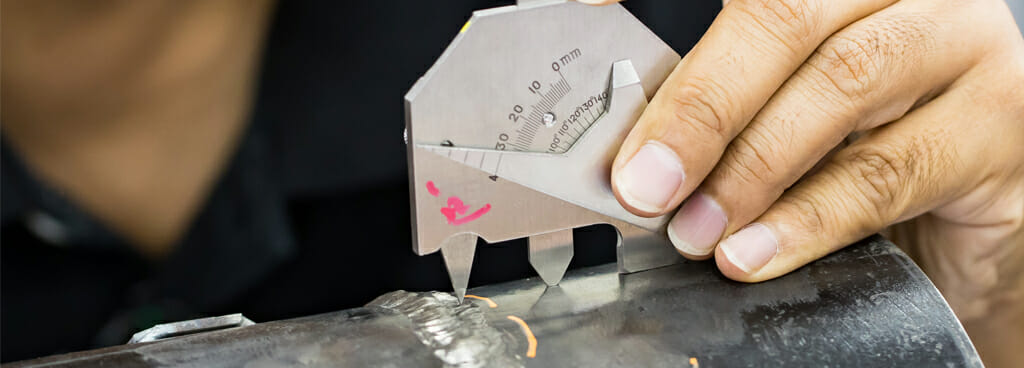
Additionally, welding inspection plays a vital duty in governing compliance. Ultimately, the role of welding assessment is vital in advertising safety, enhancing performance, and protecting investments in commercial infrastructure.
Typical Welding Defects
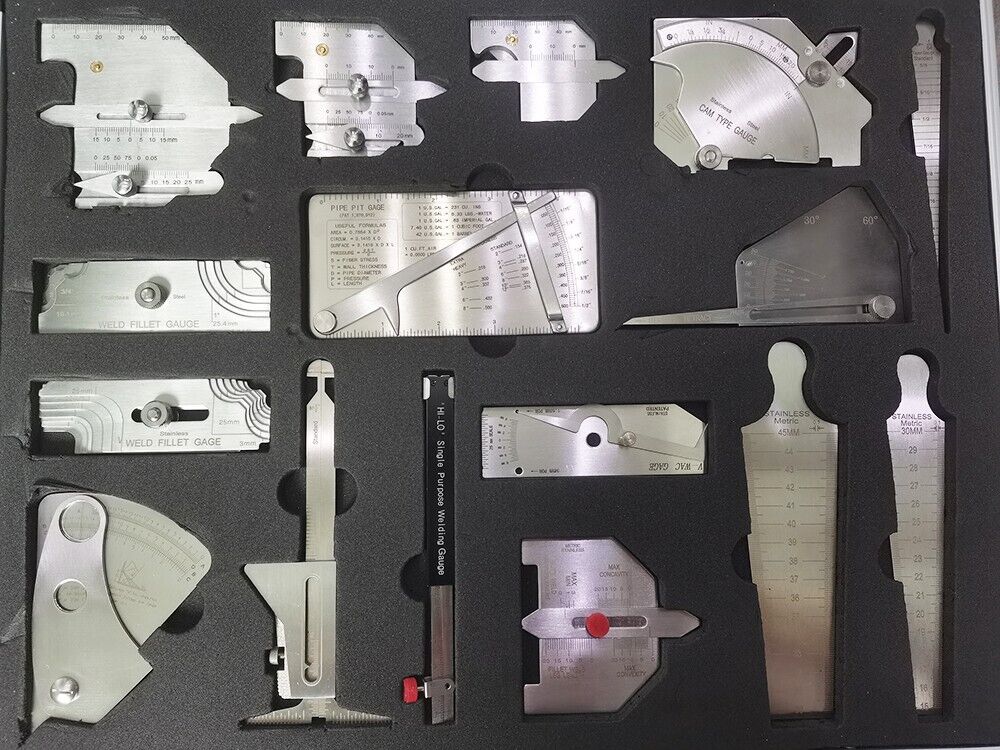
Among one of the most prevalent problems is porosity, characterized by small gas pockets entraped within the weld metal. This occurs because of impurities or inappropriate protecting gas, compromising the weld's strength. One more considerable issue is insufficient combination, where the weld metal falls short to bond appropriately with the base product, potentially causing structural weaknesses.
Splits can likewise establish during or after the welding process, typically connected to thermal tensions or incorrect cooling rates. Furthermore, damaging, where the base steel is worn down along the weld bead, can weaken the joint and is typically triggered by excessive heat input or wrong technique.
Additionally, lack of infiltration occurs when the weld metal does not reach the origin of the joint, resulting in inadequate strength. Recognizing these typical defects is important for examiners and welders alike to make sure that welded structures meet safety and performance standards, ultimately preventing potential failures in industrial applications.
Advantages of Normal Examinations
Normal inspections work as a critical guard in making certain the dependability and long life of welded structures. These evaluations identify possible defects and weak points that may jeopardize the integrity of welds, enabling timely removal before issues escalate. By implementing a structured examination regimen, organizations can dramatically minimize the threat of devastating failures that may lead to pricey downtime, devices substitute, or even mishaps.
In addition, routine assessments add to enhanced top quality control throughout the welding procedure. By sticking to a consistent examination routine, companies can make sure that their welding techniques satisfy recognized high quality benchmarks and ideal methods. This not just promotes a society of responsibility but additionally motivates continuous improvement among welding personnel.
In addition, routine examinations promote much better upkeep preparation. By recognizing damage early, organizations can strategically schedule substitutes and fixings, minimizing disruption to procedures. This proactive strategy eventually causes extensive possession life expectancy and boosted overall productivity.
Lastly, a commitment to routine examinations can enhance a business's reputation in the sector. Clients and stakeholders progressively value organizations that focus on security and quality, thereby enhancing count on and potentially leading to raised service opportunities.
Industry Specifications and Regulations
Adhering to industry requirements and guidelines is a basic element of welding evaluation that matches the benefits of normal evaluations. These criteria, established by companies such as the American Welding Society (AWS) and the American Society of Mechanical Engineers (ASME), offer a framework for best techniques in welding procedures, materials, and evaluation strategies. Conformity with these regulations makes sure that welds meet the called for top quality and safety criteria, significantly minimizing the danger of architectural failures.
Regulatory bodies like the Occupational Safety And Security and Health And Wellness Administration (OSHA) further impose guidelines that safeguard employees and the atmosphere throughout welding procedures. By following these developed standards, industries can enhance the integrity of their components and structures, ensuring they do as meant under numerous functional conditions.
Furthermore, adherence to industry criteria promotes consistency in quality control, promoting smoother interaction among stakeholders and regulatory agencies. This positioning not only reduces obligation threats however likewise boosts the credibility of companies in open markets. Eventually, conformity with welding standards and guidelines is not simply a lawful responsibility; it is an essential investment in safety, efficiency, and long-lasting operational success.
Future Trends in Welding Assessment
As markets proceed to advance, the future of welding examination is positioned to incorporate innovative modern technologies that enhance accuracy and performance. Among one of the most considerable trends is the adoption of automation and robotics in examination procedures. Automated systems can perform assessments swiftly, decreasing human error and enhancing throughput in manufacturing settings.
Moreover, the integration of expert system (AI) and artificial intelligence algorithms will certainly make it possible for predictive analytics, allowing read the full info here for real-time analyses and aggressive maintenance my explanation (Welding Inspection Gilbert Arizona). By evaluating data from previous inspections, these innovations can determine patterns that might suggest prospective failures, therefore expanding the lifespan of welded components
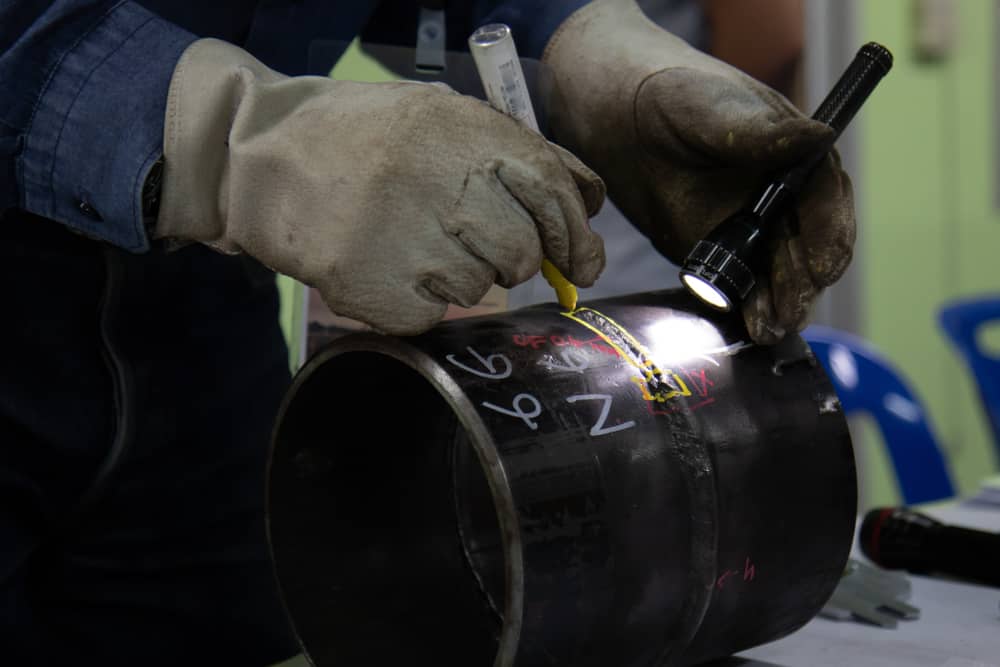
In addition, the pattern in the direction of digitalization will certainly lead to boosted data administration systems that assist in far better monitoring, reporting, and conformity with industry standards. In recap, the future of welding examination is identified by technical advancements that assure to significantly boost dependability, safety, and operational performance in different commercial applications.
Verdict
In conclusion, welding evaluation serves an essential feature in making certain the honesty and longevity of welded frameworks throughout numerous commercial applications. As improvements in modern technology continue to develop, the future of welding examination promises increased precision and efficiency, ultimately adding to the long life of critical infrastructures.
Welding assessment offers as a vital line of protection in industrial applications, making sure the architectural honesty and dependability of welded components.Welding evaluation serves as a vital guard in commercial applications, making sure that welded frameworks meet defined criteria of high quality and safety - Welding Inspection Gilbert Arizona. Inevitably, the role of welding inspection is indispensable in promoting safety and security, boosting performance, and safeguarding financial investments in industrial infrastructure
These criteria, developed by organizations such as the American Welding Culture (AWS) Read Full Report and the American Society of Mechanical Engineers (ASME), give a framework for best practices in welding processes, products, and assessment techniques.In conclusion, welding examination serves an essential function in guaranteeing the honesty and sturdiness of welded structures throughout different industrial applications.